
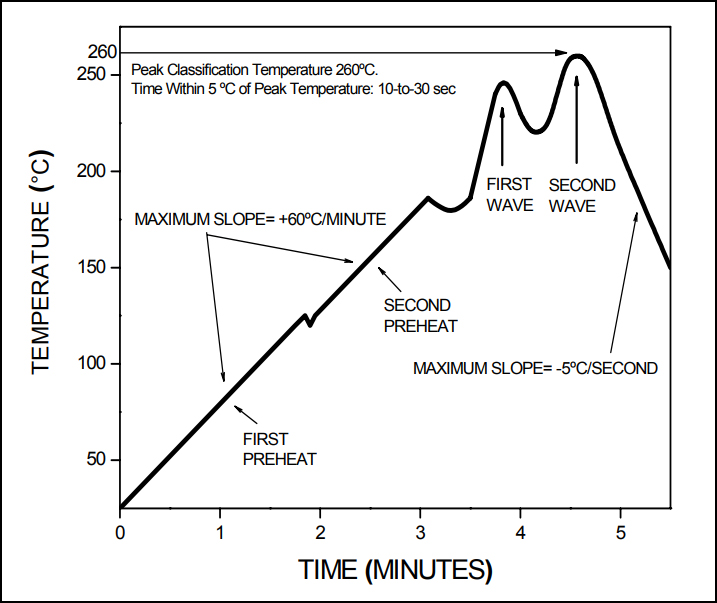
The code allows to store multiple profiles to satisfy different needs (mainly leaded or lead-free solder). After this process, the components has been fully soldering jointed with it’s SMT pad under them. So as that the SMD components is soldered on the SMT pad of the bare printed circuit board. A good explanation can be found here, or on other places on the interwebs. Reflow soldering is an important part of assembly process by which the molten state solder paste will turn to the permanent solder joints. Reflow profiles or processes that are not well optimised can lead to poor or non-wetting, damaged components or cold soldering.Īfter soldering the boards are inspected in detail. The temperature needs to follow a specific profile, the so called reflow profile. The processed board is cooling down in the last zones of the reflow oven, the solder alloy solidifies and makes the solder joints. The component that has the lowest maximum temperature allowance will define the maximum temperature. This maximum temperature must remain under the maximum allowed temperature of the components. In the third section the solder paste is melted and the process reaches its maximum temperature. The Temperature gradient is important because too quick changes of temperature can cause damage to components.ĭuring the thermal soak the flux is activated to reduce oxidation of pads and leads of components and improve wetting. The aim of the preheating stage is to accumulate heat smoothly in the board and the components. Reflow solder profiles usually have four stages, preheat, thermal soak, reflow and cooling. KOA Pb-Free Components Recommended Soldering Information and Profile. The solder profile is influenced by the number of layers in the PCB, the copper distribution on the board, the number and size of components. Solder profiles need to be optimised for each individual assembly job. Multiple segments help to get an optimised heat transfer and minimum temperature differences between different points on the PCBA. These are long convection ovens with many heating zones that together create a soldering cycle.Įach heating zone of the oven has a regulated temperature set to the solder profiles for the assembly process. The solder paste melts during this process and cools down again to create a good solder joint. During the Pick & Place operation, components are glued to the board by the solder paste.Ī reliable connection is made during the reflow soldering process.
